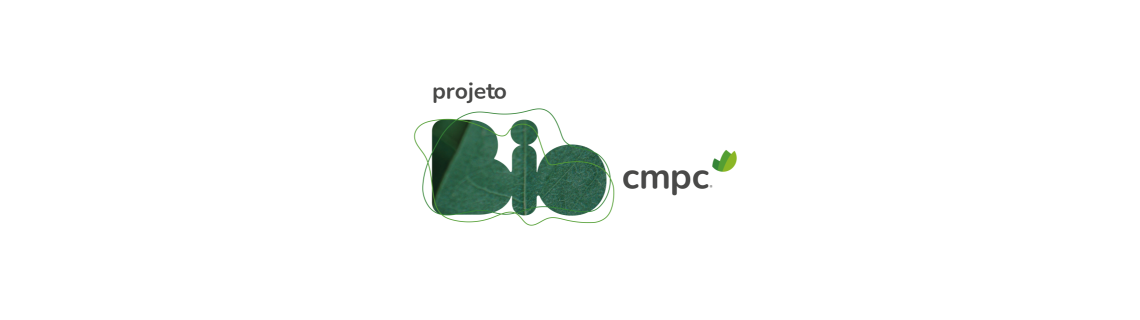
BioCMPC, a project that aims to turn the pulp mill in Guaíba into one of the most sustainable in Brazil
21 de December, 2022
Waste management, effluent treatment, atmospheric emissions, gas treatment systems and environmental management are some of the parameters that will guide the overhaul of the CMPC plant in Guaíba with a November 2023 deadline for the entire project.
In August 2021, CMPC announced a major investment in Rio Grande do Sul in southern Brazil, with a priority focus on sustainability. The operational modernization of the industrial division in Guaíba was named BioCMPC because the project seeks to make the plant one of the most sustainable in Brazil in the pulp sector, and also generate a yield gain of approximately 18% of production capacity compared to 2020 production figures.
The BioCMPC project was carefully designed based on the corporate purpose of: Creation, Coexistence and Conservation. The initiative arose after studies uncovered opportunities for improvement in terms of the environmental performance and efficiency of the division. The project interventions are divided into measures around implementing new environmental control equipment and improving existing systems, new initiatives focused on environmental management as well as operational modernization actions.
The new environmental control equipment highlights include a new electrostatic precipitator with efficiency greater than 99% in controlling particulate matter emissions, and the new recovery boiler, which will increase the amount of clean energy produced, in addition to helping eliminate 60% of greenhouse gas emissions by replacing the current coal-fired boiler. Additional notable installations include new equipment for air quality monitoring and noise control and monitoring, along with improved effluent evaluation systems. To improve the comfort of the community in terms of noise perception, the pre-existing acoustic wall on the southern edge of the plant will be extended.
The set of management actions includes a new team of environmental technicians available 24 hours a day, together with new tools for monitoring environmental KPIs with community involvement, and an Environmental Control Center (ECC) that will enable significant improvements in the environmental management of online industrial operations, an unprecedented measure in the sector.
Taken together, these measures elevate the CMPC plant in Guaíba to the status of one of the most sustainable in the country in light of the following parameters: waste management, effluent treatment, atmospheric emissions, gas treatment systems and environmental management. These projects began in September 2021, and are expected to be completed in November 2023.
With an investment of approximately USD 560 million, BioCMPC expects that the execution of the works will generate about 7,500 new jobs and about 50% of the suppliers will be local companies, making the project not only the largest ESG investment in Rio Grande do Sul, but also providing a great generation of shared value with national production chains. This is the second-largest private investment in the state’s history, second only to the creation of Guaíba 2, CMPC’s pulp production line, which was completed in 2015.
In BioCMPC, the implementation works were also planned and executed under strict control, ensuring excellent prevention and mitigation of impacts, especially designed to prevent the creation of any sort of problems for the plant’s neighbors. In addition to preferring local labor and suppliers, the support structures for the works were situated far from residential neighborhoods. Another important factor is that everyday urban mobility in the region will not be affected, as personnel, machinery and equipment access is entirely done using the company’s private access road beyond the city limits. Work hours are also limited to Monday through Friday from 8 AM to 6 PM. No work is done at night, on weekends, or on holidays.
Another important aspect in terms of circular economy principles has to do with the demolition processes that were carried out. Unlike standard practice, the structures were meticulously dismantled, and 89% of the materials were reused. Some of them were even donated to help improve schools and the community headquarters of neighborhood committees in the local area.